If you are looking for everything there is to know about liquid silicone injection moulding, this site has it all! The process, the benefits and applications This final guide has everything you need to know.
What Is Liquid silicone moulding?
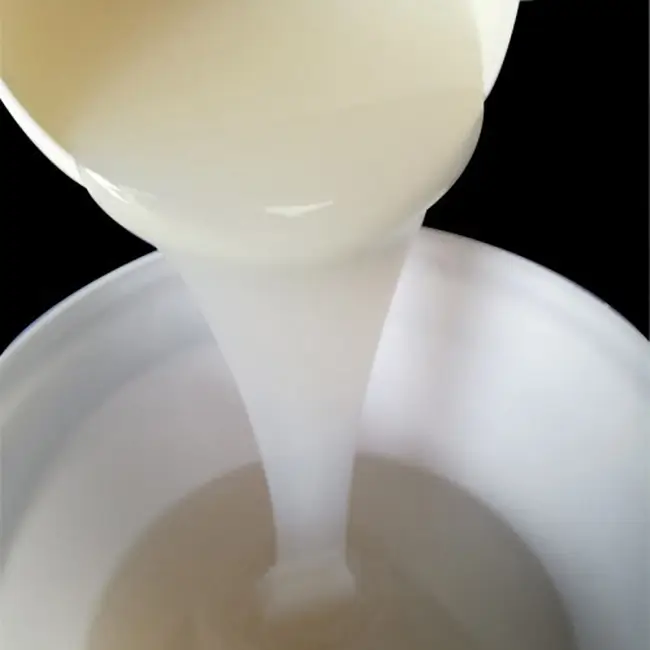
Liquid silicone molding, or liquid silicon rubber (LSR) molding for short, is a more precise and versatile process than traditional casting. This process involves pouring liquid silicone rubber in a mold cavity, making it solid and take the shape of its container. It also is very well-suited to intricate and finely detailed designs, being capable of producing complex geometries with close tolerances. In industries including medical, automotive, electronics and consumer stuffs where the flexibility combined with awesome toughness of silicone is very important liquid silicon casting is large use. The process also helps to achieve consistency and reliability in the manufacture of everything from medical implants, keypads or seals to silicone components.
What is silicone moulding used for?
Silicone molding is a multifaceted manufacturing technique used across many industries to produce all kinds of products. Silicone’s flexibility, durability, and resistance to extreme temperatures make it an excellent material for molding.
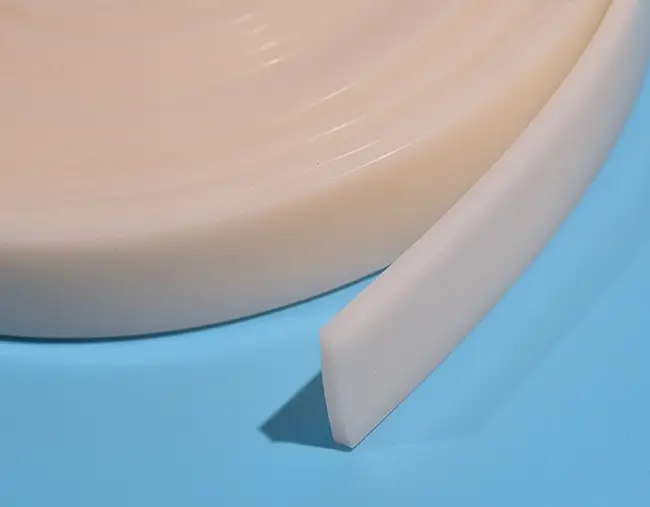
In the medical field, silicone molding is used in making things such as implants and devices because of its biocompatibility. It is used in the manufacture of gaskets, seals and other components for automobiles. Silicone molding is also widely used in electronics to create keypads and insulating components.
Furthermore, it has applications in consumer goods such as kitchenware and baby products, also novelty items of all kinds including dolls. The process can replicate fine detail, making it suitable for applications where precision and dependability are important.
What are the LSR Properties?
Liquid silicone Rubber (LSR) has a number of properties that make it attractive to users across many industries. Some key LSR properties include:
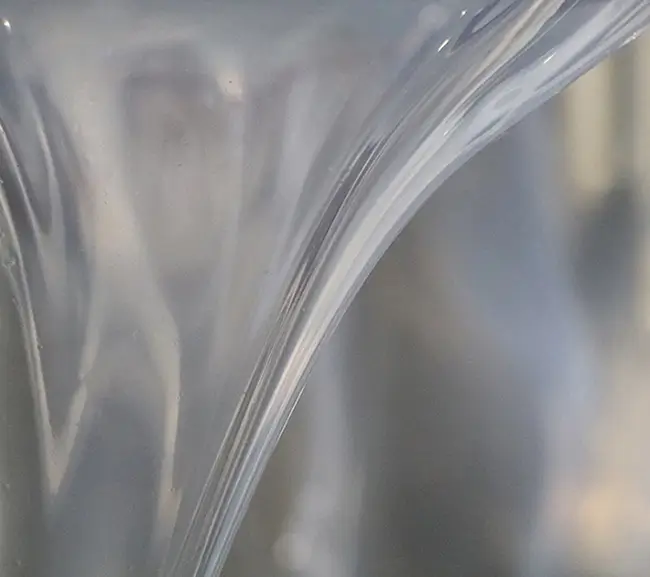
- LSR is inherently inactive and non-toxic, so it has been widely used as implants or devices for medical applications. Its electrical insulating properties are good, which makes it useful in electronics.
- LSR also has high chemical resistance, so it remains stable when exposed to different substances. In addition, its transparency combined with the ability to be pigmented gives it great design possibilities.
- Transparency and Pigmentation: LSR can be formulated to make it transparent, and it readily accepts pigments. It has an array of color options for molded products.
- Electrical Insulation: LSR possesses good electrical insulating properties, making it suitable for applications in electronic components and appliances.
- Tear and Abrasion Resistance: This durability and longevity in use comes from LSR’s high tear strength and its resistance to abrasion.
- UV and Weather Resistance: Also resistant to ultraviolet (UV) radiation and weathering, LSR is thus suited for outdoor applications.
- Liquid Injection Molding Compatibility: By taking advantage of liquid injection molding techniques, LSR can be processed into intricate and finely detailed parts with very tight tolerances.
How much does silicone rubber injection molding cost?
Many factors influence the cost of silicone rubber injection molding. You need to take into account the following factors: complexity of part design; size and intricacy of mold; type of silicone material, production volume, precision. Injection molding, in general tends to involve higher initial tooling costs as molds must be both precise and durable.
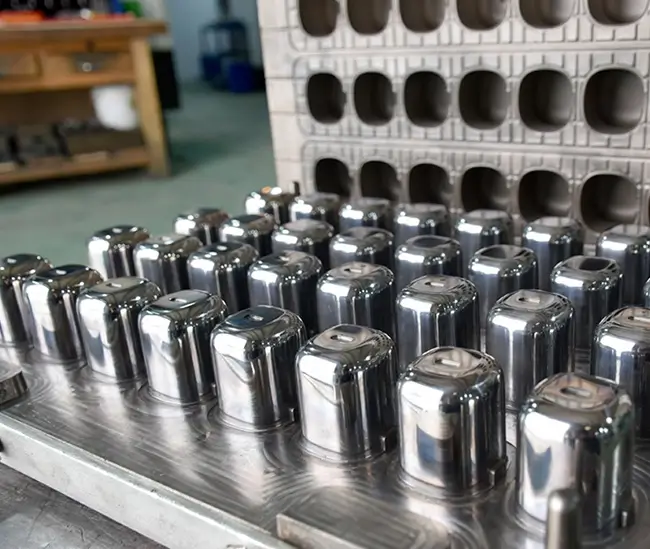
But it can be cost-effective for large production runs because the per unit price is reduced with larger quantities. What’s more, the selection of silicone material may affect costs: standard or specialized. To get an accurate price based on particular project requirements and production scale, the best solution is to work closely with manufacturers.
Industries Using LSR injection molding process
The versatility of this process is due not only to the economical benefits but also to unique properties specific LSR can impart. Some of the industries using LSR injection molding include:
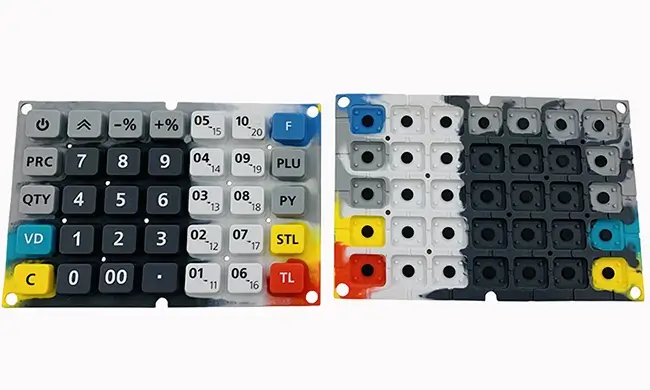
- Medical and Healthcare: Because it is biocompatible, flexible and resistant to sterilization procedures the LSR material is widely used in the medical industry for making components such as seals. gaskets, diaphragms and also use in implants themselves.
- Automotive: LSR is also used in the automobile industry to make parts such as gaskets, seals O-rings and connectors. With this combination of extreme temperature resistance and flexibility, it is also suited to automotive engineering.
- Electronics: Because of its electrical insulating properties, durability and resistance to environmental factors LSR is used in the electronics industry for keypads, insulated parts and precision components.
- Consumer Goods: Because of its flexibility, safety and ease in molding complex designs LSR is used to make a variety of goods for consumer use including cookware, baby articles and personal care items.
- Industrial Equipment: Industrial components that require resistance to the effects of harsh chemicals, temperature fluctuations and wear and tear are manufactured with LSR.
- Aerospace: In the aerospace field, however, LSR is used to produce parts that must withstand extreme conditions: high and low temperature variations; vibration; exposure to chemicals.
- Appliances: Heat and chemical resistant, LSR retains its characteristics advantageously over a long period of time. Therefore it is used in manufacturing components for household appliances.
- Toy Manufacturing: Its flexibility, safety and color are all suitable for the production of toys or novelties.
- Chemical resistance: Silicone rubber is waterproof, resists oxidation and some chemical solutions such as acids and alkali. Normal medical and healthcare-related materials can be sterilized through methods ranging from steam autoclaving to ethylene oxide (ETO), gamma, e-beam or any of a myriad number of other procedures.
- Durable: Liquid silicone rubber parts can deal well with extreme temperatures, making it an excellent choice for components to be found under the hood of automobiles and applications outdoors.
In addition to its combination of high-precision design, long service life and excellent dimensional stability (can be used in environments containing 57% sodium hydroxide), that makes LSR injection molding suitable for all industries where there are many tight tolerances in each part.
Liquid Silicone Rubber Part Production process
Typically, the production process for liquid silicone rubber (LSR) parts involves several steps following a liquid injection molding procedure. Here is a simplified overview of the LSR part production process:
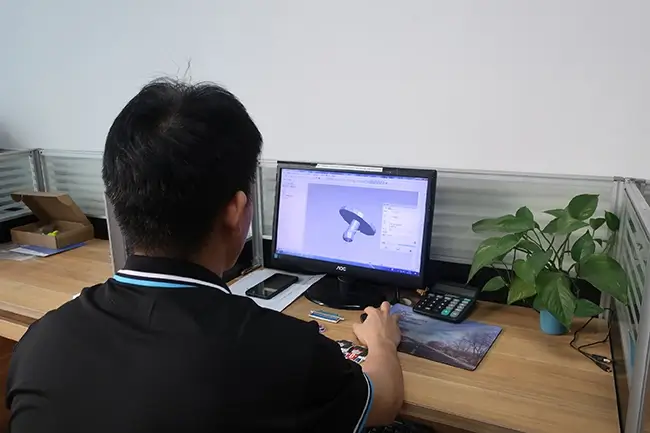
- Design: The design of the part is where it all begins. Using CAD (Computer-Aided Design) software, it is generally possible to construct a highly accurate digital image of the desired product.
- Mold Design: The part design is used to create a mold. The ply then is usually made of metal (such as aluminum or steel), cut and shaped through sensitive precision machining, so that the cavity in which liquid silicone will be injected takes shape. The mold design plays a decisive role in the part geometry.
- Preparation: The liquid silicone rubber material is prepared before injection. This means measuring and mixing the two-component LSR material (base and catalyst) in proper proportions. This mixture is usually called the A and B ingredients.
- Injection Molding: Injected into the mold cavity under high pressure is prepared LSR material. The liquid injection molding process makes it possible for the material to flow into the most detailed portions of a mold. However, the mold is then closed up and heated to promote curing (vulcanization) of the liquid silicone into its final shape.
- Curing: The mold is kept sealed and the LSR cured to a pre-set temperature for a set period of time. This step is particularly important to attain the desired physical properties of the final part.
- Demolding: After being cured, the mold opens up and out comes the finished LSR part. The part may be subjected to further post-curing or inspections in order to maintain quality.
- Post-Curing (Optional): Other applications might involve post curing to improve certain properties of the LSR, such as hardness or resistance against environmental factors.
- Inspection and Quality Control: Examine the completed parts for dimensional correctness, blemishes and general appearance.
- Trimming and Finishing: Cut back any extraneous material or flash from the LSR parts. As needed to meet specifications, other finishing processes are performed.
- Packaging: Assemble the LSR parts into a secure package for shipment or final assembly.
- High-precision, stable and complex: Injection molding for LSRs is known for its ability to produce high precision, consistent pieces that are suitable across all industries (medical, automotive electronics or consumer goods).
But precision, consistency and control are all required in this production process to ensure that the liquid silicone rubber parts conform with requirements of use.
Equipment for LSR Injection Molding machine
So the equipment for LSR (Liquid Silicone Rubber) injection molding machines includes a number of essential components designed to accommodate liquid silicone rubber’s unique properties. Here are the key elements:
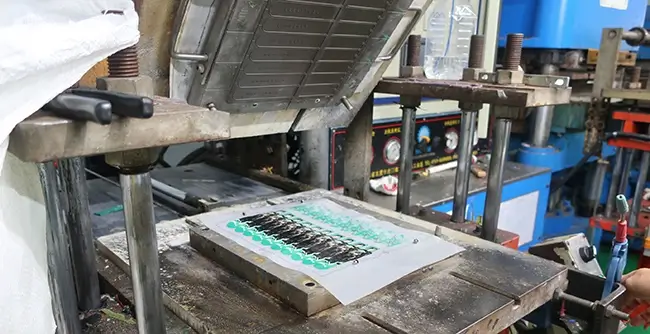
- Injection Unit – The injection unit incorporates a screw or plunger mechanism so the liquid silicone rubber material may be melted, metered and injected into the mold.
- Mold – The mold, which is of great importance and usually made out of metal (aluminum or steel), shapes the LSR into what one desires. It encompasses the cavity that gives shape to the part.
- Clamping Unit – A clamping unit keeps the mold in place during injection, forming a tight seal. This unit serves to hold the mold shut in response to pressure generated during injection.
- Heating Elements – For this reason, LSR injection molding machines are furnished with heating elements to control and maintain the temperature of the LSR material incurring during curing. Precision temperature control is crucial to obtaining suitable material properties.
- Temperature Control System – This system regulates and controls the temperature of such parts as the barrel, mold, spray mechanism and other critical areas to provide constant curing while preventing overheating.
- Cooling System – After curing, a cooling device is employed to cool the mold. With solidified LSR part removed from it without distortion.
- Automated Control System – The entire LSR injection molding process is controlled by an automated control system. It sets the injection parameters, monitors temperature and decides when to move from one phase of operation into another. This all contributes toward making the process precise, repeatable and accurate in its results.
- Hydraulic System (Optional) – LSR injection molding machines employ a hydraulic system to generate the required force for clamping and inject processes.
- Material Handling System – The LSR material is delivered and prepared by this system, to maintain accurate mixing proportions of the base components with catalyst.
- Injection Nozzle or Sprue System -The injection nozzle or sprue system pumps the LSR material from the injection unit into the mold cavity.
Combined together they make it possible for the LSR injection molding machine to produce high-quality, precision silicone rubber parts quickly and with great degree of reproducibility. The equipment is designed to meet the special characteristics of liquid silicone rubber, so that it can be widely used in fields including medicine, automobiles and electronics as well.
Applications of LSR Injection Molding
Because LSR (Liquid Silicone Rubber) can create precision components with unique characteristics, this process is widely used across industries.
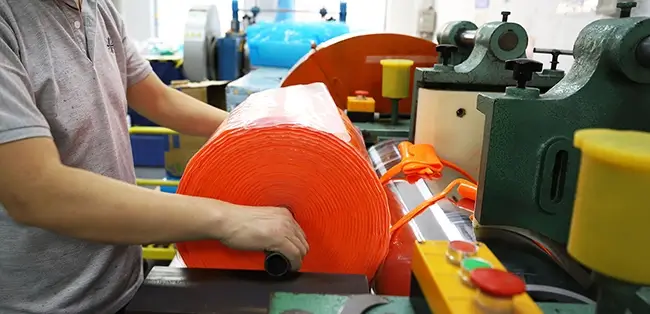
medical field
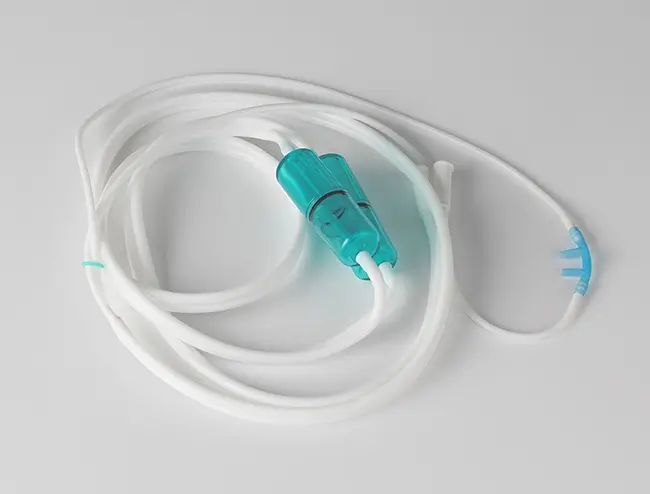
In the medical field LSR is used for biocompatible and sterilizable parts like seals, surgical instruments.
automotive applications
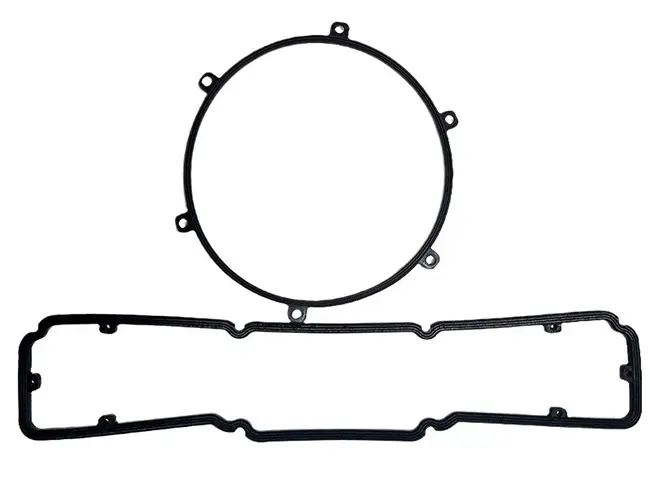
LSR is resistant to extremes of temperature and used in making seals, gaskets etc. for automotive applications.
electronics
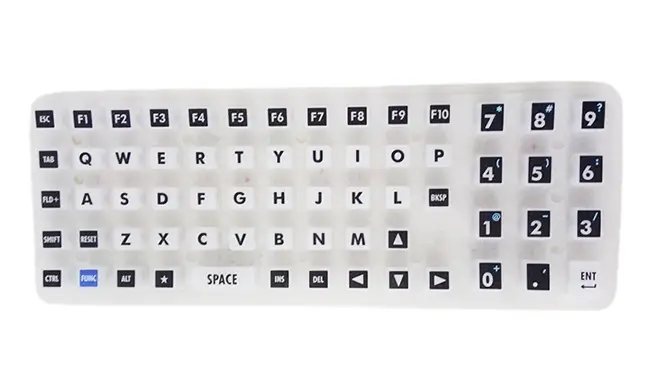
In electronics, LSR is selected for its electrical insulating function in elements like keypads.
kitchenware
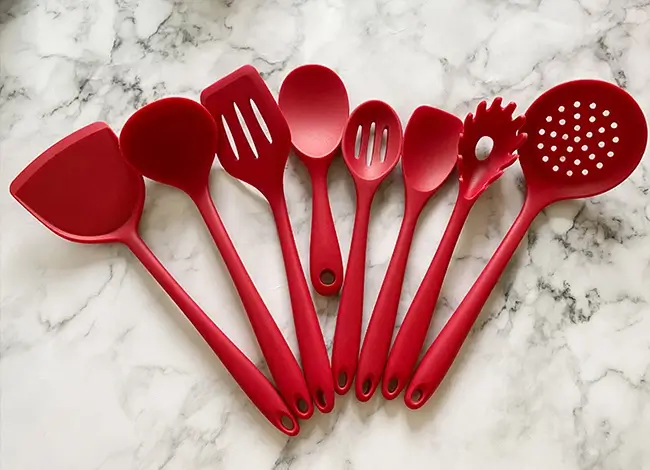
In kitchenware, baby products and personal care items it is LSR’s flexibility that benefits consumer goods.
aerospace systems
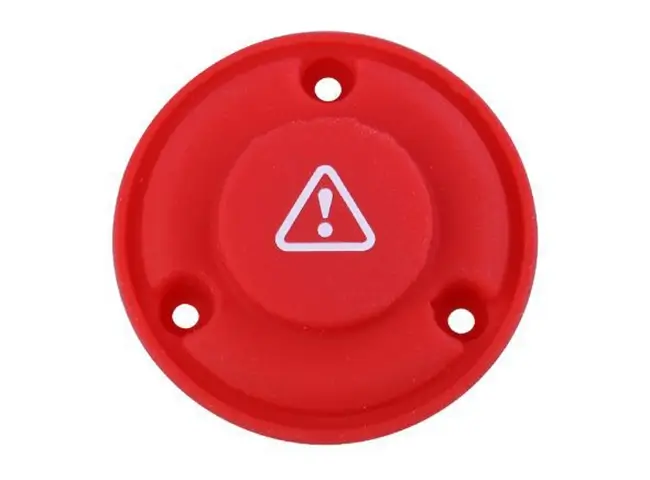
LSR is used to make components of aerospace systems facing extreme conditions.
industrial equipment
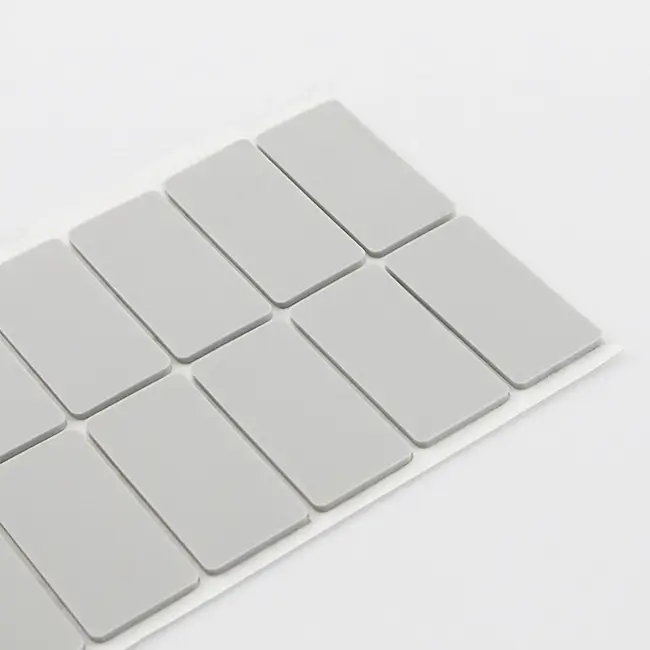
For example, LSR is mainly used in the chemical resistance of seals and gaskets for industrial equipment.
production of baby products
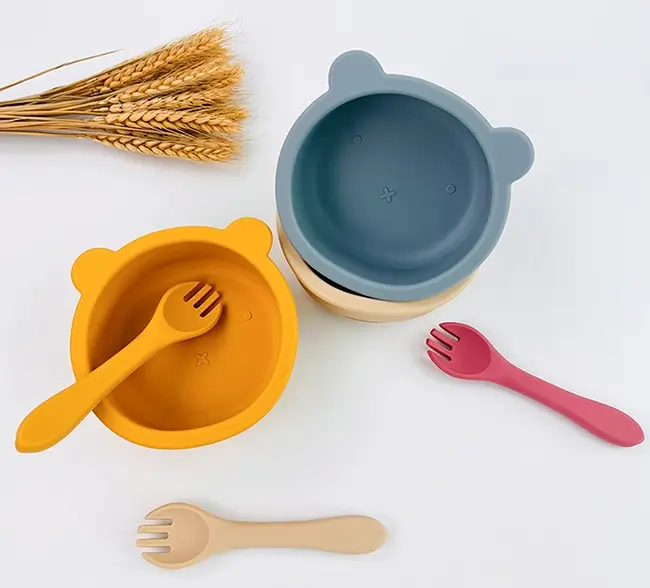
Safety, strength and precision: LSR injection molding is used not only for medical components but also in the production of baby products lighting components and keypads.
Because of the LSR’s superior adaptability, it is often used in applications requiring flexibility, durability and biocompatibility.
LIM Silicone Molding Vs. Compression Molding
Two different ways of molding silicone are Liquid Injection Molding (LIM) and Compression Molding. Each method has its advantages and applications.
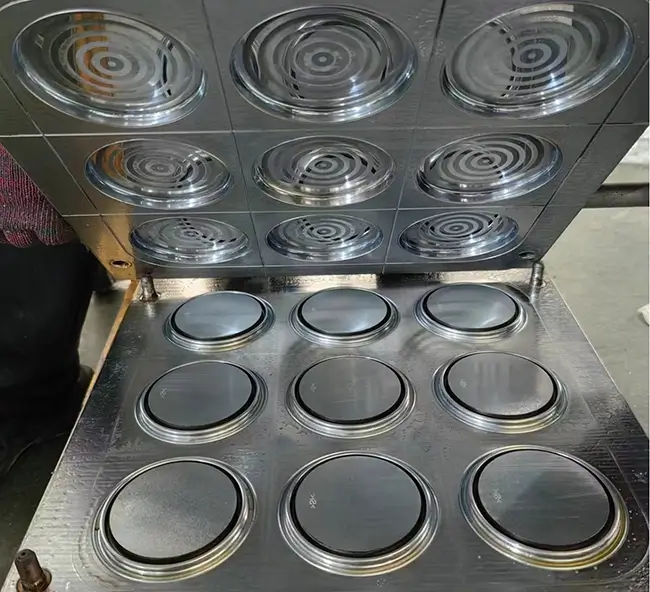
Injection molding (LIM) involves forcing liquid silicone rubber into a closed mold under high pressure to obtain parts of extreme detail and complexity with virtually no waste. With tight tolerances and suitable for intricate designs, it’s perfect for applications such as medical devices and electronic components.
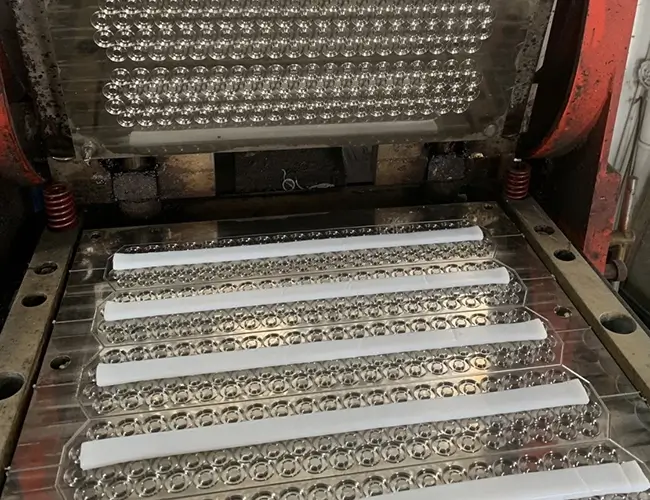
In Compression Molding, on the other hand, a pre-measured silicone compound is directly placed into an open mold which is then closed. The final product is subjected to heat and pressure, making the alternative cheaper for simple shapes but less suitable for complex models.
Because LIM focuses on the areas of precision and complexity, Compression Molding is often chosen for simpler shapes in larger volumes because it entails lower die tooling costs.
Whether to go with LIM or Compression Molding depends on project particulars, complexity of the part and production volumes.
What items are compression molded?
Compression molding is commonly used for manufacturing electric socket switches and faceplates. Medical equipment parts – Many plastic or rubber parts used in medical equipment use compression moulding including syringe stops.
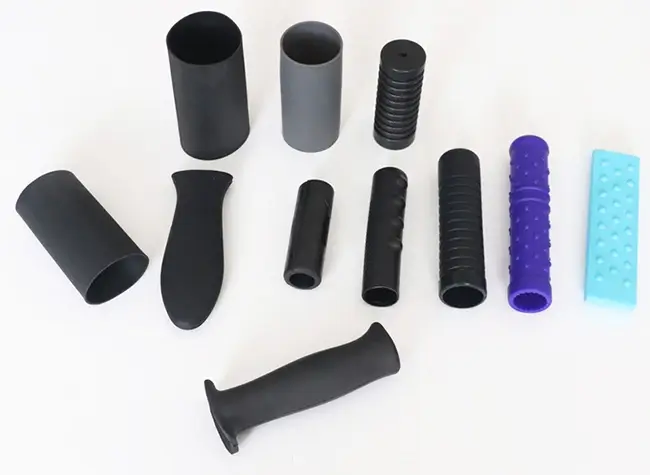
Compression molding is widely used for many products in a number of different industries. Because the compression molding process is efficient at producing high-quality, consistent parts in large numbers and low costs, products such as rubber seals or gaskets are commonly compressed formed.
Besides, many simple automotive components are compression molded for their durability and economy>such as engine mounts and bushings. Compression molding is used in the consumer goods sector for products which have a particularly simple design such as handles, coarse sorts of grips and some industrial parts. In sum, compression molding is flexible and goes into the manufacture of a lot of different rubber and plastic parts.
Advantages of Liquid silicone rubber molding
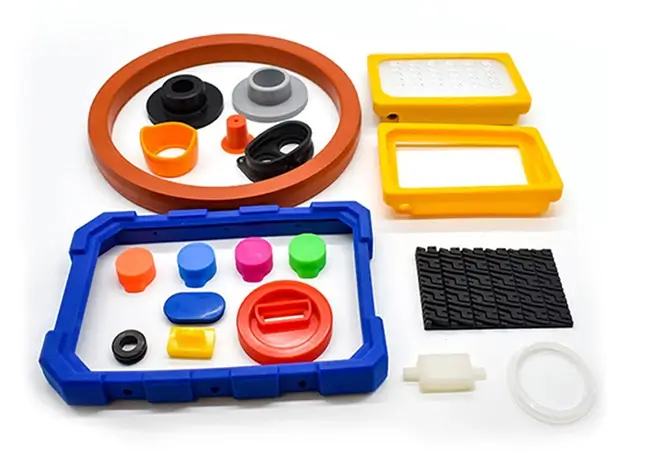
- Precision and Detail: With LSR Molding, complex and highly precise parts can be produced.
- Consistency: This automated process provides uniform and reproducible results, which reduces variations between parts.
- Versatility: LSR materials can be tailored to different properties, such as flexibility, transparency and toughness.
- Biocompatibility: LSR is also nontoxic, so it can be used for medical applications like implants and healthcare devices.
- Efficiency: The process can produce in large volume, with short cycle times.
- Durability: LSR parts have outstanding wear resistance and long service life.
- Temperature Resistance: LSR materials are stable over a wide range of temperatures.
- Reduced Waste: The more precise molding is, the less waste of materials. This reduces costs and helps protect our environment.
- Color Customization: It is simple to color LSR, making a wide range of colors possible.
- Minimal Finishing Requirements: LSR molding leads to low flash, so finishing requirements are reduced.
Disadvantages of Liquid silicone rubber molding
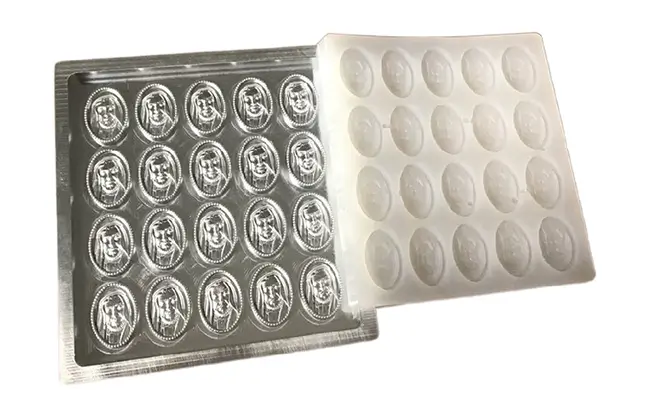
- High Initial Tooling Costs: Making liquid silicone rubber molds can be expensive.
- Limited Material Options: In terms of the range of available liquid silicone rubber materials in comparison to other molding processes, there might be a narrower choice.
- Cycle Time: Curing in liquid silicone rubber molding may increase cycle times, which affects production speed overall.
- Skill and Training: LSR molding requires highly skilled operators, and adequate training must be provided to ensure standard oversight.
- Waste in Start-up and Shutdown: During the startup and shutdown phases of the molding machine, there may be material waste.
- Not Ideal for Large Parts: LSR molding isn’t the cheapest option for very large parts or low-volume production.
- Limited in Part Thickness: Certain complex parts are difficult to maintain a consistent wall thickness.
- Post-Curing Requirements: Some applications may require extra post-curing steps which increase the turnaround time.
- Limited Compatibility with Certain Additives: Some additives are incompatible with LSR formulations, which limits material choices.
- Dependency on Suppliers: Maintaining stable supply chain depends crucially on diversity of LSR materials.
Summary
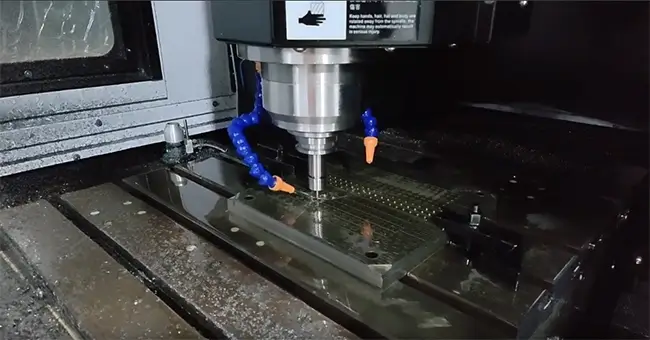
“The Ultimate Guide to Liquid Silicone Injection Moulding: “Everything You Need to Know” is a comprehensive guide covering every aspect of liquid silicone injection molding from start to finish. The guide covers everything from the basic principles of the process to advanced techniques, and serves as a valuable resource for both beginners in manufacturing and veteran technicians. It explores the subtleties of material preparation, injection molding machinery and mold design that are required to produce high-precision silicone rubber components which will last for a long time. Moreover the guide also covers in detail all aspects of LSR materials, their properties and uses across industries which have excellent insulating properties and also electrical properties which some have the most consistent lsr parts and numerous other techniques in ejector pins to human tissue and other silicon parts. It is an indispensable reference for anyone wanting to go deeply into liquid silicone injection molding and its widespread applications with high consistency rubber, have a liquid silicone rubber injection, which all of them have mechanical properties, mixing process, some have hardness range, curing process, tight tolerances and then either it could have experience of its liquid nitrogen, hot mold, and the often can also withstand extreme temperatures by demonstrated superior compatibility in the cushioning pads.
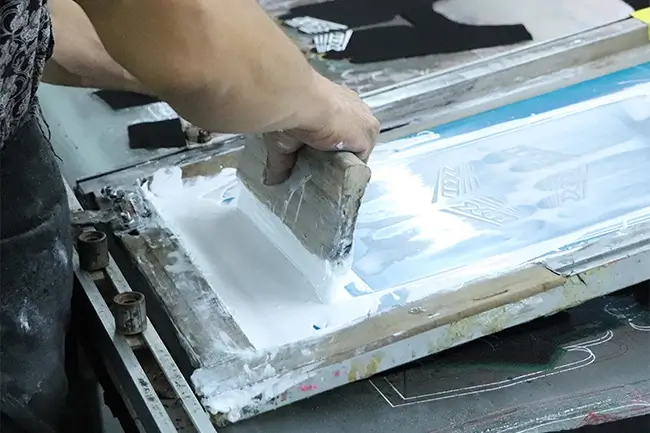
With a focus on clarity and depth, the goal of this guide is to provide readers with knowledge which can help them successfully traverse LSR molding. Whether learning about the benefits of LSR, understanding what might go wrong, or exploring individual industry applications-the guide is a complete and convenient reference for anyone who wants to grasp this art and science to the other materials just like in injection rate in medical applications.