Custom Printed
Silk screen printing
Silk screen printing is the first printing method. Screen printing needs to open a screen, so it is also called screen printing. Generally, the silk screen printing ink will be thicker and the printed pattern will have high color saturation.
The silicone ink used has good tensile color fastness, and the silk screen can only print one color at a time. If you need to register the color, first print the first color, then bake it, adjust the position of the screen, and then print the second one. color.
Silk screen printing can also print relatively thin lines and is also suitable for large-area printing. The disadvantage is that multi-color printing is too slow and the production capacity is not high, because the color registration has high technical requirements for workers. Products that can only be printed on a flat surface
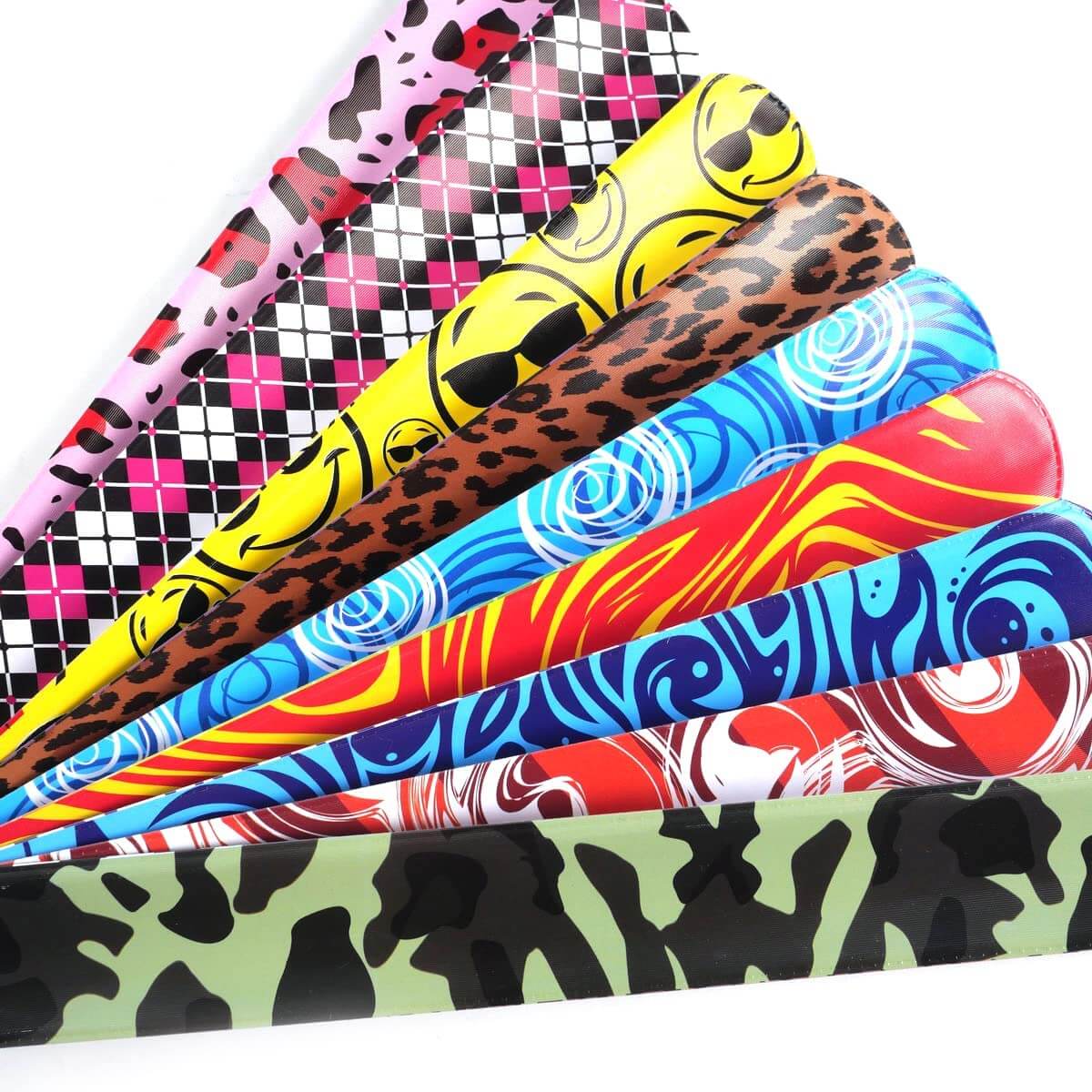
pad printing silicon
Pad printing silicon is a steel plate, which is printed by machine. The principle is to engrave the logo on the steel plate. When the pad printer scratches once, the ink will gather in the engraved place, and the silicone head above it can be printed on the product with the ink dipped in it.
Silicone ink has good tensile color fastness, and can print products with curved surfaces. The advantage of pad printing is that the printing speed is fast, and it can do color registration of several colors of the logo at the same time. The disadvantage is that compared with silk screen printing, the printing area is small, the ink is slightly thinner, and the color saturation of the pattern is less.

Silicone digital printing
Silicone digital color printing is directly printed on the surface of silicone with a digital printer, so the background color of color printing products is generally required to be white, otherwise the printed color will be distorted.
Digital printing uses CMYK ink, low color saturation, no tension, average color fastness, and low productivity! Advantages do not need to open version suitable for small batch orders.
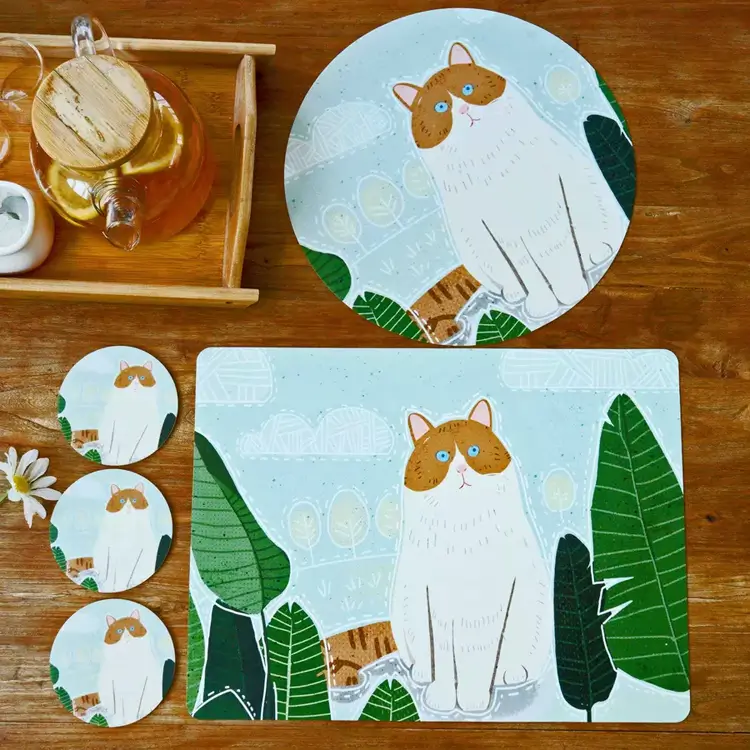
dispensing
The glue dispenser is used to point the color of the liquid silica gel to the corresponding position of the mold, bake it and then put it into the solid silica gel for molding.
The advantages are good color saturation and good tensile fastness, but the disadvantages are expensive mold, low precision, and average production capacity.
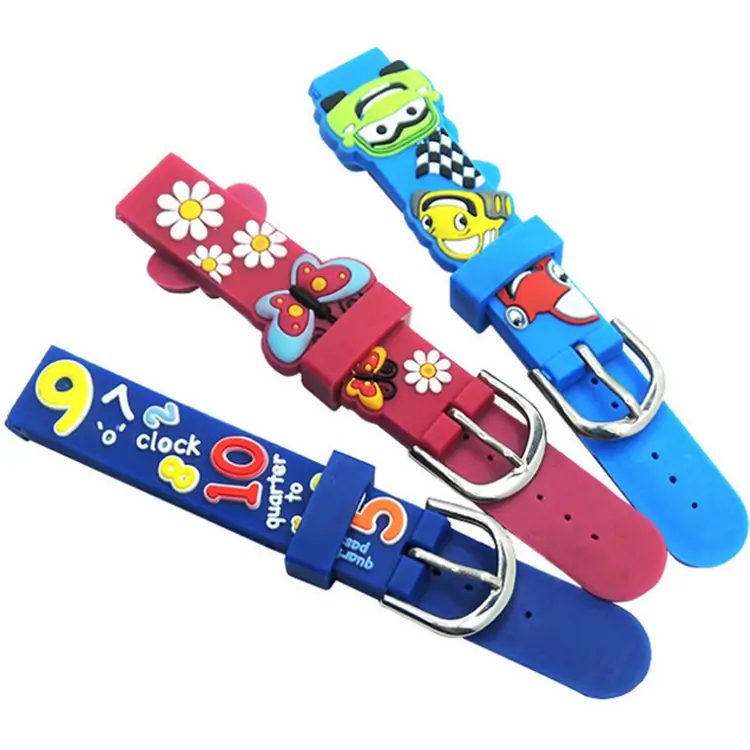
Silicone transfer printing
Silicone transfer is divided into thermal transfer and water transfer. Both print the pattern on the transfer film first. After the silicone product is treated with a treatment agent, the pattern is attached to the surface of the silicone by heat transfer or water transfer.
Advantages Suitable for large surface level surface structure products. However, the transfer film is relatively expensive for machine printing, suitable for products with relatively large order quantities, and the color fastness to tensile force is average.
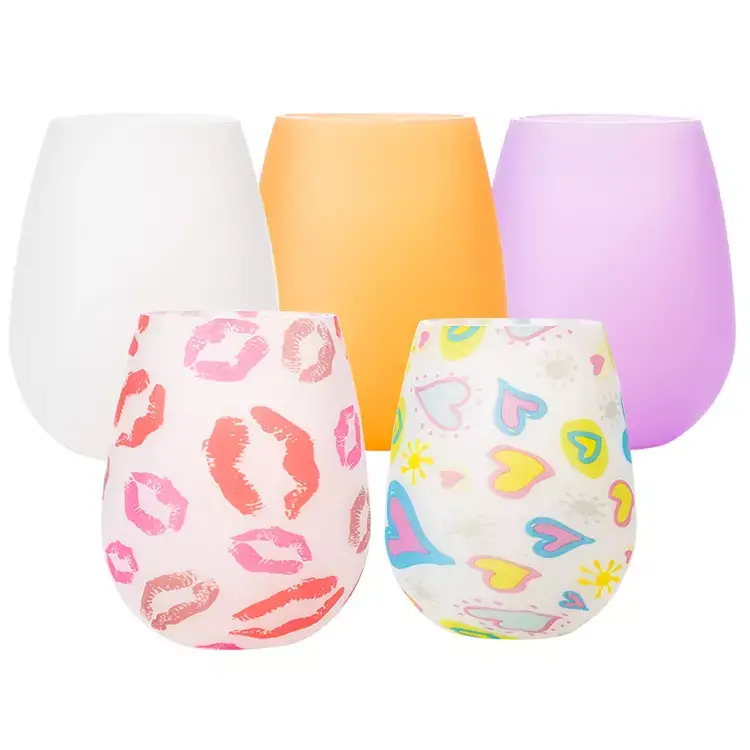
IMD / IMR
Multi-color silicone integrated molding, commonly known as silicone film internal transfer, is to print the pattern on the transfer film first, which can be machine-printed or silk-screened, and then position the patterned transfer film in the mold and mold it together with the silicone. Finally, tear off the film. .
The advantage of transfer printing inside the silicone film is that flexible size orders can be made, three-dimensional patterns can be made, the cost is not high, the pulling force is good, and the color fastness is good. The disadvantage is that it cannot be used on large surfaces.
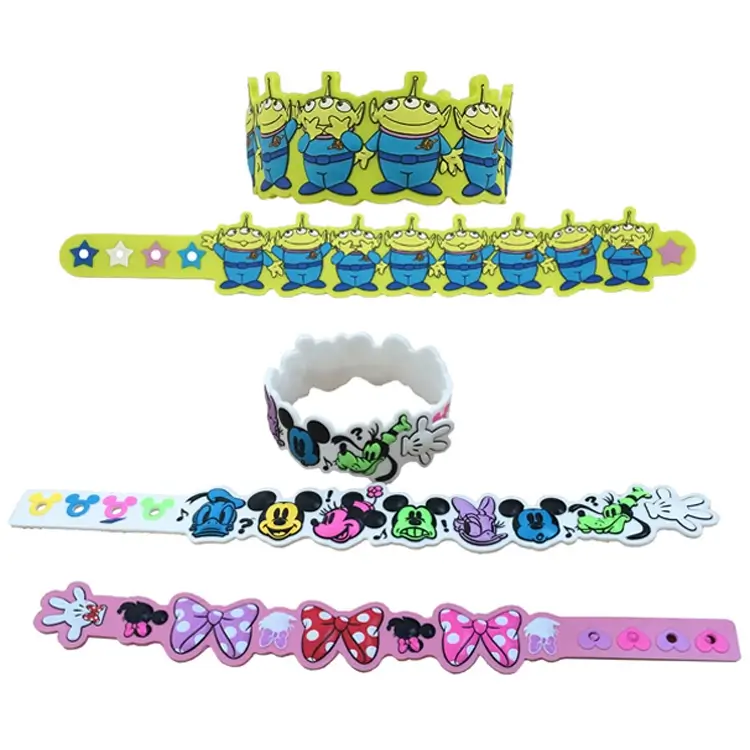