As a material, silicone rubber has long been a popular choice for a wide range of applications. However, with the advent of liquid silicone rubber (LSR) technology, the benefits of silicone have been amplified. LSR has gained widespread popularity for its versatility, high-quality output, and cost-effectiveness in producing custom silicone parts. In this article, we will explore the benefits of LSR for custom silicone parts, the different types of custom silicone molds, the advantages of custom silicone molds, and the applications of LSR molding in different industries.
Introduction to Liquid Silicone Rubber (LSR)
LSR is a type of silicone rubber that is used in a wide range of applications. It is a two-part liquid material that is cured into a solid form. LSR is known for its high strength, flexibility, and durability, and it is widely used in the production of custom silicone parts. LSR is also known for its excellent resistance to extreme temperatures, chemicals, and UV radiation.
LSR is a popular choice for the production of custom silicone parts due to its ability to produce high-quality, precision parts with tight tolerances. LSR can be molded into complex shapes and designs that are difficult to achieve with other materials. LSR is also known for its high repeatability, which makes it an ideal material for the production of large quantities of parts.

Benefits of LSR for Custom Silicone Parts
One of the primary benefits of LSR for custom silicone parts is its versatility. LSR can be molded into a wide range of shapes and designs, making it an ideal material for the production of custom silicone parts. LSR is also known for its high precision and accuracy, which makes it an ideal material for the production of parts with tight tolerances.
LSR is also known for its excellent resistance to extreme temperatures, chemicals, and UV radiation. This makes it an ideal material for the production of custom silicone parts that will be exposed to harsh environments. LSR is also known for its high strength, flexibility, and durability, which makes it an ideal material for the production of parts that will be subjected to high stress and strain.
Another benefit of LSR for custom silicone parts is its cost-effectiveness. LSR can be molded into complex shapes and designs with high precision and accuracy, which makes it an ideal material for the production of large quantities of parts. The high repeatability of LSR also makes it an ideal material for the production of parts with consistent quality.
Liquid Silicone Molding (LSM) vs. Injection Molding
LSM and injection molding are two popular methods for molding silicone rubber. LSM is a process that uses liquid silicone rubber to produce parts, while injection molding uses solid silicone rubber pellets that are melted and injected into a mold.
LSM has several advantages over injection molding. LSM can produce parts with high precision and accuracy, which makes it an ideal method for the production of custom silicone parts. LSM can also produce parts with tight tolerances, which makes it an ideal method for the production of parts that require high levels of precision.
LSM also has a shorter cycle time than injection molding, which makes it an ideal method for the production of large quantities of parts. LSM can also produce parts with consistent quality, which makes it an ideal method for the production of parts that require consistent quality.
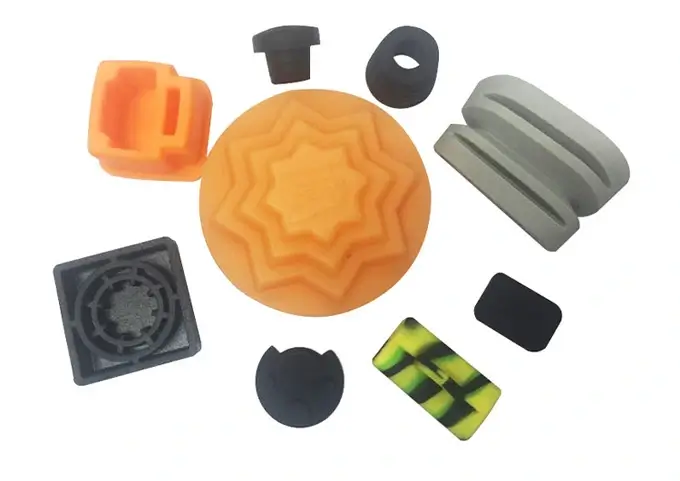
The Process of LSR Molding
The process of LSR molding involves several steps. The first step is the preparation of the mold. The mold is prepared by cleaning and coating it with a release agent. The next step is the mixing of the two-part LSR material.
The mixed LSR material is then injected into the mold using a molding machine. The LSR material is then cured into a solid form. The cured part is then removed from the mold and inspected for quality.
Types of Custom Silicone Molds
There are several types of custom silicone molds that can be used in the production of custom silicone parts. The most common types of custom silicone molds include compression molds, transfer molds, and injection molds.
Compression molds are used to produce parts with large dimensions or complex shapes. Transfer molds are used to produce parts with intricate designs or thin walls. Injection molds are used to produce parts with tight tolerances or complex geometries.

Advantages of Custom Silicone Molds
Custom silicone molds have several advantages over standard molds. Custom silicone molds can be designed to produce parts with specific geometries, which makes them ideal for the production of custom silicone parts. Custom silicone molds can also be designed to produce parts with complex shapes or thin walls, which makes them ideal for the production of parts that are difficult to produce with standard molds.
Custom silicone molds also have a shorter lead time than standard molds. Custom silicone molds can be designed and produced in a fraction of the time it takes to produce standard molds. This makes custom silicone molds an ideal choice for the production of parts that require a quick turnaround time.
Choosing the Right Custom Silicone Mold Manufacturer
When choosing a custom silicone mold manufacturer, it is important to consider several factors. The first factor to consider is the experience of the manufacturer. A manufacturer with experience in the production of custom silicone molds will be able to produce high-quality molds that meet your specific requirements.
The second factor to consider is the quality of the molds produced by the manufacturer. The molds produced by the manufacturer should be of high quality and should be able to produce parts with tight tolerances and complex geometries.
The third factor to consider is the cost of the molds. The cost of the molds should be reasonable and should not exceed your budget. It is important to get quotes from several manufacturers to compare prices and choose the one that offers the best value for money.

Applications of LSR Molding in Different Industries
LSR molding has several applications in different industries. In the automotive industry, LSR molding is used to produce parts such as gaskets, seals, and hoses. In the medical industry, LSR molding is used to produce parts such as tubing, catheters, and implants.
In the electronics industry, LSR molding is used to produce parts such as keypads, connectors, and seals. In the consumer goods industry, LSR molding is used to produce parts such as phone cases, kitchen utensils, and toys.
Custom Silicone Products and Rubber Parts
Custom silicone products and rubber parts have several applications in different industries. In the automotive industry, custom silicone products and rubber parts are used to produce parts such as gaskets, seals, and hoses. In the medical industry, custom silicone products and rubber parts are used to produce parts such as tubing, catheters, and implants.
In the electronics industry, custom silicone products and rubber parts are used to produce parts such as keypads, connectors, and seals. In the consumer goods industry, custom silicone products and rubber parts are used to produce parts such as phone cases, kitchen utensils, and toys.
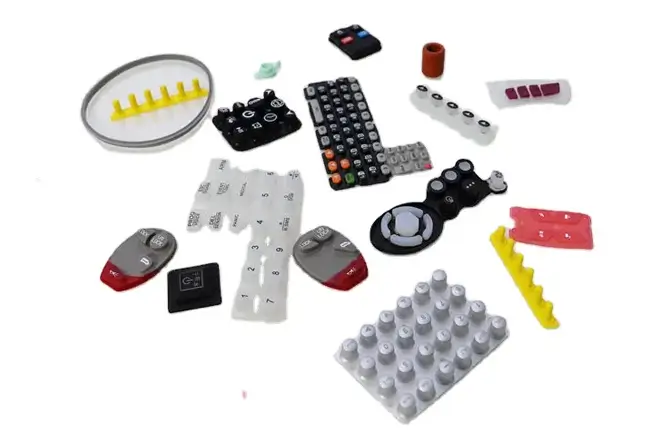
Maintenance and Care for Silicone Parts
Silicone parts require proper maintenance and care to ensure their longevity and performance. Silicone parts should be cleaned regularly with mild soap and water. Harsh chemicals and abrasives should be avoided, as they can damage the silicone material.
Silicone parts should also be stored in a cool, dry place away from direct sunlight. Exposure to extreme temperatures and UV radiation can damage the silicone material and reduce its lifespan.
The Future of LSR Molding Technology
The future of LSR molding technology looks bright. Advances in LSR technology are expected to lead to the development of new materials and processes that will further enhance the versatility, quality, and cost-effectiveness of LSR molding.
New materials such as liquid silicone foam and liquid silicone gel are expected to offer new possibilities for the production of custom silicone parts. New processes such as multi-shot molding and overmolding are expected to offer new possibilities for the production of parts with complex geometries and multiple materials.

Conclusion
LSR is a versatile and cost-effective material for the production of custom silicone parts. LSR has several advantages over other materials, including its high precision, accuracy, and repeatability, its excellent resistance to extreme temperatures, chemicals, and UV radiation, and its ability to produce parts with tight tolerances and complex geometries.
LSR molding is a popular method for producing custom silicone parts due to its high-quality output and cost-effectiveness. Custom silicone molds have several advantages over standard molds, including their ability to produce parts with specific geometries and their shorter lead time.
When choosing a custom silicone mold manufacturer, it is important to consider the experience, quality, and cost of the manufacturer. LSR molding has several applications in different industries, and the future of LSR molding technology looks bright with the development of new materials and processes.
If you’re interested in learning more about LSR molding and custom silicone parts, please contact us today.