Silicone products have become an essential part of various industries due to their durability, flexibility, and versatility. As a custom silicone manufacturer, it is critical to ensure that the products you produce meet the highest standards of quality. Quality control plays a significant role in achieving this objective, and in this article, we will discuss the importance of quality control in custom silicone production.
I. Introduction
Custom silicone production is a complex process that involves multiple steps, from material selection to final inspection. Quality control is a critical aspect of this process as it helps ensure that the final product meets the required specifications and standards. In this article, we will discuss why quality control is important in custom silicone production, the various quality control methods used, and the benefits of implementing a robust quality control system.
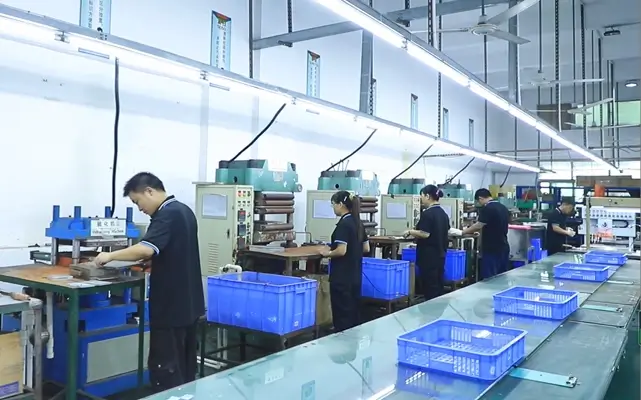
II. The Importance of Quality Control in Custom Silicone Production
Quality control is an essential aspect of custom silicone production for the following reasons:
- Ensuring Product Consistency: Consistency is a crucial factor in custom silicone production, and quality control helps ensure that the products produced are consistent in terms of their shape, size, color, and other attributes. Consistency is particularly important in industries such as medical, aerospace, and defense, where product quality is critical.
- Meeting Customer Requirements: Custom silicone products are designed to meet specific customer requirements, and quality control helps ensure that the products produced meet these requirements. Quality control helps ensure that the products are of the required quality, are safe to use, and meet the desired performance standards.
- Maintaining Brand Reputation: Quality control helps maintain the reputation of the manufacturer by ensuring that the products produced are of high quality, meet the required standards, and are safe to use. A manufacturer with a reputation for producing high-quality products is more likely to attract repeat business and new customers.
- Reducing Production Costs: Quality control helps identify and address quality issues early in the production process, reducing the risk of producing defective products. This, in turn, helps reduce production costs by minimizing the need for rework, scrap, and product recalls.
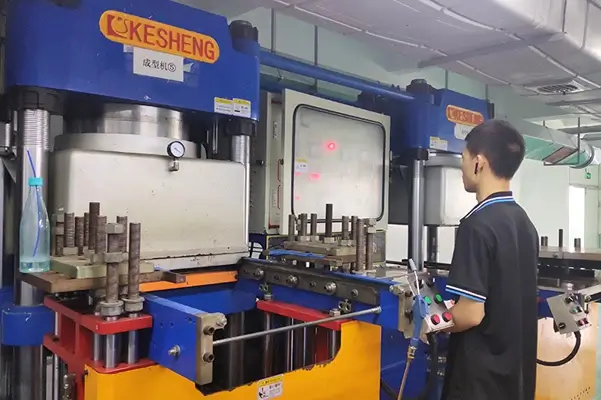
III. Quality Control Methods in Custom Silicone Production
Various quality control methods are used in custom silicone production to ensure that the final product meets the required standards. These methods include:
- Material Testing: Material testing is conducted to ensure that the raw materials used in custom silicone production meet the required specifications. Material testing involves testing the physical and chemical properties of the raw materials, such as tensile strength, elongation at break, hardness, and viscosity.
- Process Control: Process control involves monitoring and controlling the various stages of custom silicone production to ensure that the products produced are of the required quality. This includes monitoring the injection molding process, curing time, and temperature, among other factors.
- Final Inspection: Final inspection is conducted to ensure that the final product meets the required specifications and standards. Final inspection involves visual inspection, dimensional measurement, and functional testing, among other methods.
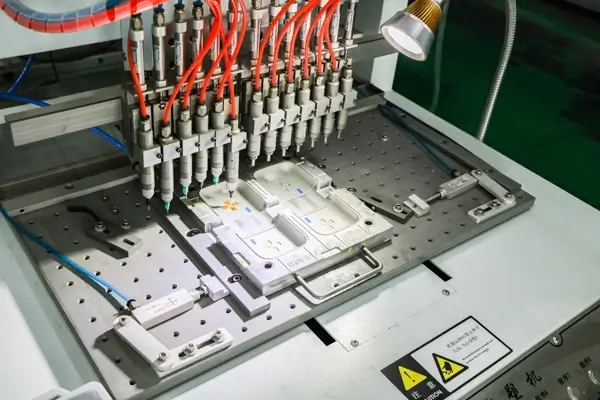
IV. Benefits of Implementing a Robust Quality Control System
Implementing a robust quality control system in custom silicone production offers several benefits, including:
- Improved Product Quality: A robust quality control system helps ensure that the products produced meet the required standards and specifications, resulting in improved product quality.
- Reduced Production Costs: A quality control system helps reduce production costs by minimizing the need for rework, scrap, and product recalls.
- Increased Customer Satisfaction: A robust quality control system helps ensure that the products produced meet customer requirements, resulting in increased customer satisfaction.
- Enhanced Brand Reputation: A manufacturer with a reputation for producing high-quality products is more likely to attract repeat business and new customers, resulting in an enhanced brand reputation.
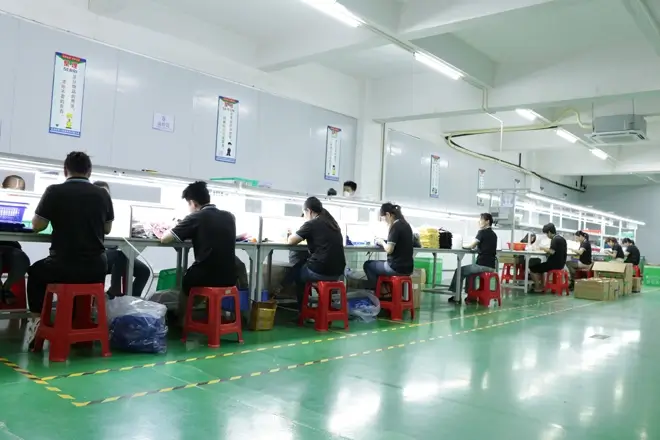
V. Conclusion
Custom silicone production is a complex process that requires careful attention to quality. In addition to the benefits of improved product quality and customer satisfaction, implementing a robust quality control program can also help companies reduce costs associated with waste, rework, and customer returns. By catching potential issues early in the production process, manufacturers can prevent larger problems down the line and ultimately save money in the long run.
In conclusion, quality control is a critical component of custom silicone production. By implementing a comprehensive quality control program, manufacturers can ensure that their products meet the highest standards of quality and reliability. This, in turn, can lead to improved customer satisfaction, increased sales, and reduced costs. As the demand for high-quality silicone products continues to grow, manufacturers who prioritize quality control will be well-positioned to succeed in this competitive market.