As a manufacturing assistant, I have observed the increasing demand for silicone in various industries. The unique properties of silicone make it an ideal material for use in different applications such as medical devices, electronics, automotive, construction, and consumer goods. However, despite its widespread use, many people still lack a comprehensive understanding of silicone, its manufacturing process, and its applications. In this ultimate guide to silicone manufacturing, I will provide an in-depth analysis of the different aspects of silicone, from its origin as a silicon mixture to the production of silicone rubber.
Introduction to Silicone Manufacturing
Silicone is a synthetic polymer made from silicon, carbon, oxygen, and hydrogen. It was first introduced in the 1940s and has since become a critical material in various industries. Silicone is known for its unique properties, such as its excellent thermal stability, resistance to chemicals, and electrical insulation. These properties make it an ideal material for use in harsh environments, extreme temperatures, and high-performance applications.
The manufacturing process of silicone involves synthesizing silicon from silicon dioxide (SiO2) through the reduction process. The silicon is then combined with other elements such as carbon, oxygen, and hydrogen to form a silicone polymer. The manufacturing process of silicone is complex and requires specialized equipment and expertise.
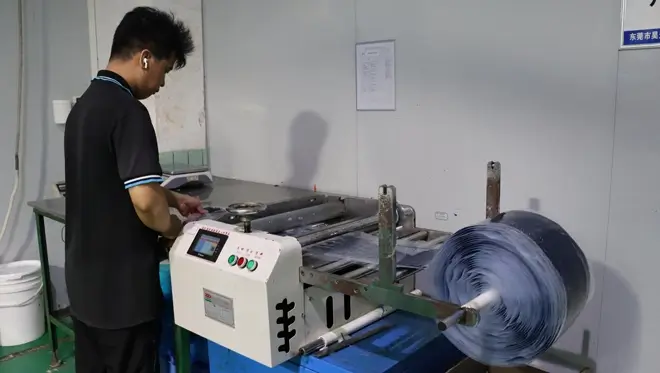
Understanding Silicone: Silicon Mixtures vs. Silicone Rubber
Silicone is generally classified into two types: silicon mixtures and silicone rubber. Silicon mixtures are the raw materials used in the production of silicone rubber. They are made by combining silicon with other elements such as carbon, oxygen, and hydrogen. Silicon mixtures are used in the production of silicone rubber through a process known as vulcanization.
On the other hand, silicone rubber is the final product of the manufacturing process. It is a synthetic elastomer made from silicon mixtures. Silicone rubber is known for its excellent properties such as high thermal stability, resistance to chemicals, and low surface tension. These properties make it an ideal material for use in various applications, including medical devices, automotive, construction, and consumer goods.
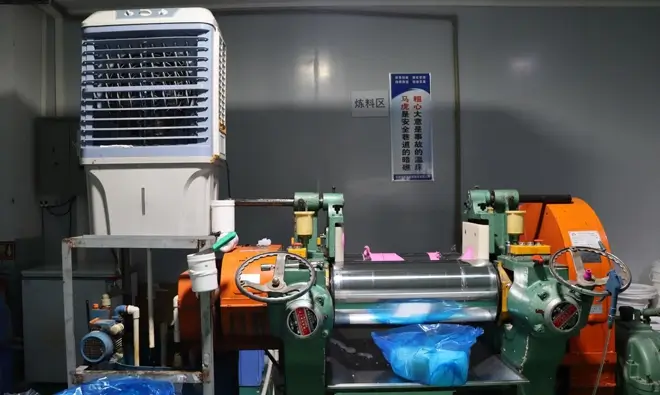
The Manufacturing Process of Silicone Rubber
The manufacturing process of silicone rubber involves several steps, including mixing, curing, and molding. The first step is the mixing of the silicon mixture with other additives such as catalysts, crosslinkers, and fillers. The mixture is then heated and cured to form a solid material. The curing process involves the use of heat or radiation to initiate the crosslinking of the polymer chains.
After curing, the silicone rubber is molded into various shapes using different techniques such as injection molding, compression molding, and extrusion. The molding process is critical as it determines the final properties of the silicone rubber. The molded parts are then subjected to post-curing processes such as annealing and heat treatment to improve their mechanical properties.
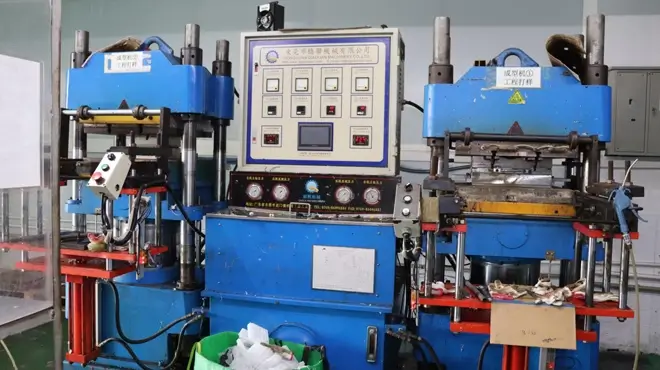
Applications and Uses of Silicone
Silicone is used in various applications due to its unique properties. In the medical industry, silicone is used in the production of medical devices such as implants, catheters, and prosthetics. Its biocompatibility and resistance to high temperatures make it an ideal material for use in medical applications.
In the electronics industry, silicone is used as an encapsulant for electronic components. Its excellent thermal stability and electrical insulation properties make it an ideal material for use in harsh environments.
In the automotive industry, silicone is used in the production of gaskets, seals, and hoses. Its resistance to high temperatures, chemicals, and weathering make it an ideal material for use in automotive applications.
In the construction industry, silicone is used in the production of sealants, adhesives, and coatings. Its excellent resistance to weathering and chemicals makes it an ideal material for use in construction applications.
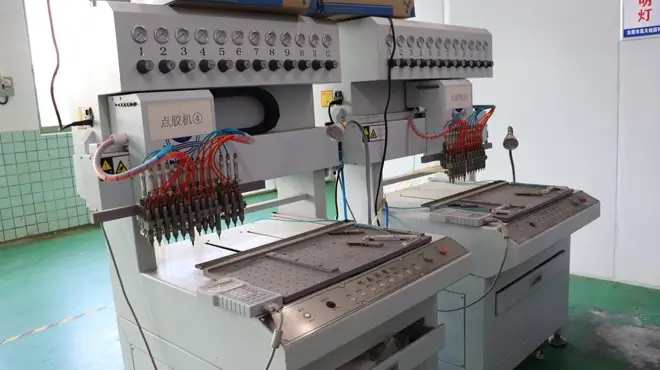
Silica vs. Silicone: What’s the Difference?
Silica and silicone are two terms that are often used interchangeably, although they are entirely different. Silica is a natural mineral found in rocks and soils. It is also known as silicon dioxide (SiO2). On the other hand, silicone is a synthetic polymer made from silicon, carbon, oxygen, and hydrogen.
Silica is used in various applications, including the production of glass and ceramics. It is also used as a filler in the production of silicone rubber.
Silicone vs. Silicon: Why the Confusion?
Silicone and silicon are often confused due to their similar names. Silicon is a chemical element with the symbol Si and atomic number 14. It is a metalloid with semiconductor properties and is widely used in the electronics industry.
On the other hand, silicone is a synthetic polymer made from silicon, carbon, oxygen, and hydrogen. It is used in various applications due to its unique properties such as high thermal stability, resistance to chemicals, and electrical insulation.
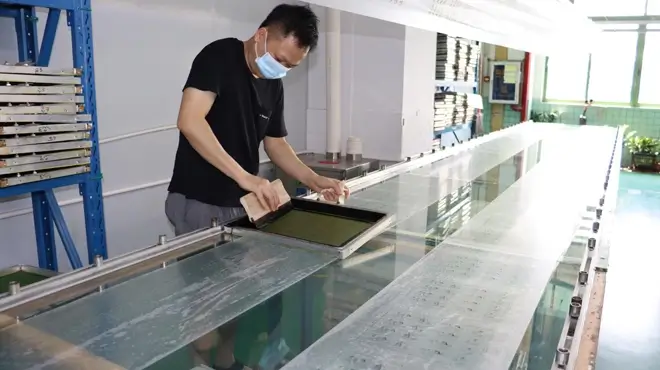
The Importance of Quality Control in Silicone Manufacturing
Quality control is critical in silicone manufacturing to ensure that the final product meets the required specifications and standards. Quality control involves several steps, including testing the raw materials, monitoring the manufacturing process, and testing the final product. Quality control helps to identify defects and ensure that the final product is of high quality and meets the required standards.
Key Players in the Silicone Manufacturing Industry
The silicone manufacturing industry is dominated by a few key players, including Dow Corning, Wacker Chemie AG, Momentive Performance Materials, and Shin-Etsu Chemical. These companies have a significant market share and are known for their high-quality products and innovative solutions.
Emerging Trends and Innovations in Silicone Manufacturing
The silicone manufacturing industry is constantly evolving, and there are several emerging trends and innovations in the industry. One of the emerging trends is the use of silicone in 3D printing. 3D printing with silicone offers several advantages, including the ability to produce complex shapes and structures.
Another emerging trend is the use of silicone in the production of smart materials. Smart materials are materials that can change their properties in response to external stimuli such as temperature, light, or pressure. Silicone is an ideal material for use in smart materials due to its unique properties.
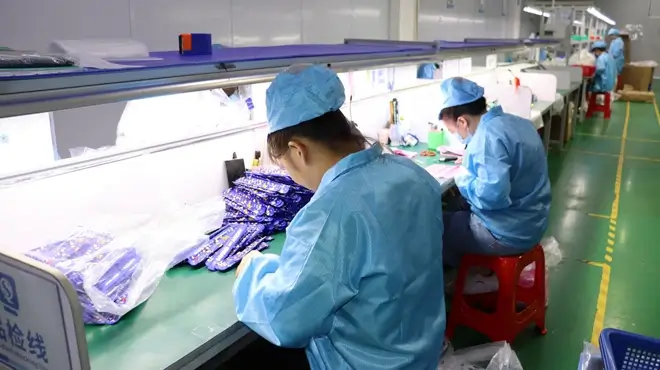
Conclusion: The Future of Silicone and Its Role in Manufacturing
Silicone is a critical material in various industries due to its unique properties such as high thermal stability, resistance to chemicals, and electrical insulation. The manufacturing process of silicone is complex and requires specialized equipment and expertise. Quality control is critical in silicone manufacturing to ensure that the final product meets the required specifications and standards.
The future of silicone is bright, with several emerging trends and innovations in the industry. Silicone is expected to play a significant role in the manufacturing industry due to its unique properties and versatility. As a manufacturing assistant, I believe that silicone will continue to be an essential material in various industries and will drive innovation and growth in the manufacturing industry.