In a world where aesthetics reign supreme, the marriage of beauty and functionality has never been more captivating. Enter the realm of In-Mold Decoration (IMD), a mesmerizing technique that has revolutionized the world of silicone products. With a touch of artistry and a dash of ingenuity, IMD unveils a realm of endless possibilities, where silicone transcends its conventional boundaries. In this article, we embark on a journey to explore the enchanting world of IMD and discover how it breathes new life into silicone creations, elevating them to the realm of true artistry. Prepare to be captivated as we unravel the secrets behind IMD’s transformative power and witness how it shapes the future of silicone products.
A. Brief Explanation of In-Mold Decoration (IMD)
In the realm of manufacturing, where innovation continually pushes the boundaries of design, In-Mold Decoration (IMD) has emerged as a mesmerizing technique that adds a touch of enchantment to silicone products. IMD is a process that seamlessly integrates art and functionality, transforming ordinary silicone items into captivating works of art. By infusing intricate designs directly into the mold, IMD allows for a harmonious union of form and function, resulting in stunning visual aesthetics that endure the test of time. This article delves into the world of IMD and explores how this technique breathes life into silicone creations, captivating the senses and enchanting consumers.
B. Importance of Aesthetics in Silicone Products
In today’s consumer-driven market, aesthetics play a vital role in the success of products, and silicone-based items are no exception. Silicone, with its unique properties of flexibility, durability, and versatility, has found its way into various industries, ranging from consumer electronics to household products and automotive components. While functionality is crucial, aesthetics have become equally significant in capturing the attention and desires of discerning consumers. Silicone products that exhibit exceptional visual appeal have the power to evoke emotions, make lasting impressions, and elevate user experiences. Recognizing this importance, manufacturers are turning to IMD as a game-changing technique that unleashes the artistic potential of silicone, redefining what is possible and captivating the hearts of consumers worldwide.
Stay tuned as we embark on a captivating journey into the world of IMD, exploring the enchanting process that elevates silicone products to the realm of true artistry.
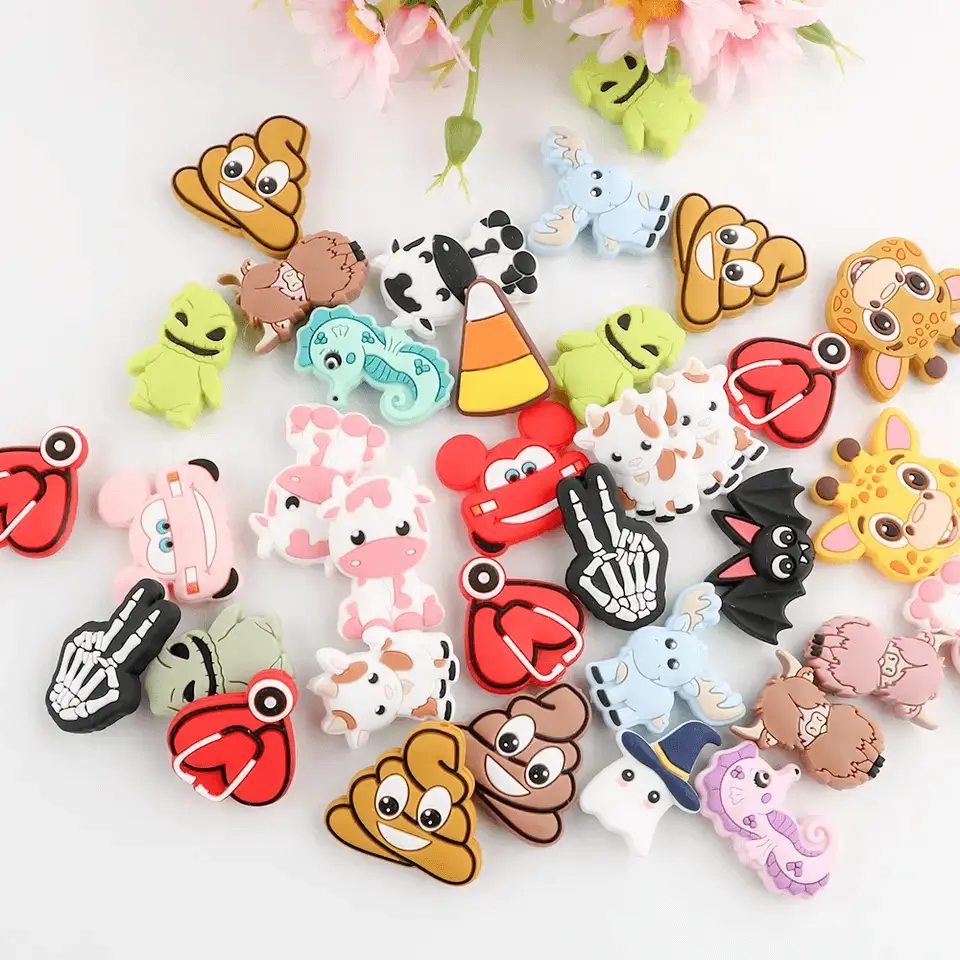
II. Understanding IMD
A. Definition and Process of IMD
In-Mold Decoration (IMD) is a sophisticated manufacturing technique that enhances the visual appeal of silicone products by seamlessly integrating decorative elements during the molding process. It involves placing a pre-printed film or foil, containing intricate designs or patterns, into the mold cavity before injecting molten silicone. The combination of heat and pressure allows the silicone to bond with the film, transferring the design onto the product’s surface. The result is a beautifully decorated silicone item with a smooth and durable finish that is both visually striking and functional.
B. Key Benefits of Using IMD in Silicone Product Manufacturing
IMD offers numerous advantages that have made it a preferred choice for enhancing silicone products:
- Design Freedom: IMD unlocks a world of design possibilities by enabling intricate patterns, textures, and graphics that were once difficult to achieve through traditional methods. Manufacturers can explore limitless options to create eye-catching silicone products that stand out in the market.
- Seamless Integration: Unlike post-production decoration techniques, IMD seamlessly integrates the decorative elements with the silicone material during the molding process. This eliminates the need for additional assembly steps and ensures a flawless, integrated design that won’t peel, fade, or wear off over time.
- Time and Cost Efficiency: IMD streamlines the production process by eliminating the need for separate decoration or finishing steps. The design is applied directly to the product during molding, reducing manufacturing time and cost associated with post-decoration processes like painting, printing, or labeling.
- Enhanced Durability: The IMD process creates a protective barrier for the design, making it highly resistant to scratches, abrasions, and fading. The design is encapsulated within the silicone, ensuring long-lasting visual appeal, even in demanding environments or with frequent use.
- Consistency and Reproducibility: IMD ensures consistent and reproducible decoration across multiple silicone products. The precision of the molding process allows for uniform distribution of the design, maintaining a high level of quality and aesthetic appeal throughout the production batch.
By harnessing the power of IMD, manufacturers can elevate silicone products to new artistic heights while reaping the benefits of enhanced design possibilities, efficiency, and durability. Join us as we dive deeper into the captivating world of IMD and uncover its transformative impact on silicone manufacturing.
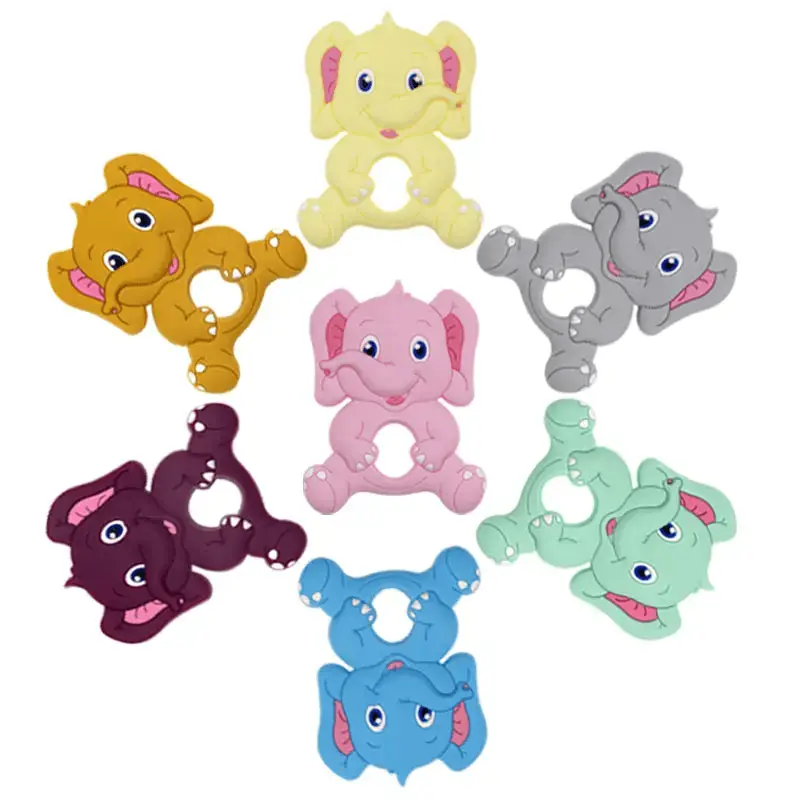
III. Enhancing Design Possibilities
A. Exploring the Limitless Design Options Offered by IMD
In-Mold Decoration (IMD) is a gateway to a world of boundless design possibilities for silicone products. With IMD, manufacturers can unleash their creativity and bring intricate, visually captivating designs to life. The technique allows for precise replication of complex patterns, textures, gradients, and even 3D effects directly onto the surface of silicone items. From sleek and minimalist aesthetics to bold and vibrant visuals, IMD empowers designers to push the boundaries of imagination, transforming silicone into a canvas for artistic expression. Whether it’s intricate filigree patterns, lifelike textures, or captivating abstract designs, IMD opens up a realm of design freedom that captivates the eyes and sparks delight in consumers.
B. Case Studies Showcasing Creative and Intricate IMD Designs in Silicone Products
Let’s explore some captivating case studies that demonstrate the remarkable possibilities of IMD in silicone product manufacturing:
- Tech Accessory Marvel: Imagine a smartphone case adorned with a mesmerizing IMD design, showcasing an intricate mosaic of colors and textures. IMD allows for precise replication of detailed artwork, ensuring a seamless integration of the design onto the silicone surface. The result is a stunning tech accessory that not only provides protection but also becomes a visual delight.
- Automotive Elegance: IMD finds its place in the automotive industry, where silicone components like buttons, knobs, and trim pieces can be transformed into sophisticated works of art. From elegant woodgrain textures to sleek metallic finishes, IMD enables silicone products to exude luxury and refinement, enhancing the interior aesthetic of vehicles.
- Kitchenware Charm: Silicone kitchen utensils and accessories can be elevated to a new level of visual appeal with IMD. Imagine a silicone spatula adorned with a vibrant floral pattern or a set of silicone coasters featuring intricate geometric designs. IMD allows for the seamless integration of these captivating patterns onto silicone, turning everyday kitchen essentials into delightful decorative elements.
These case studies highlight just a fraction of the creative possibilities that IMD offers for silicone products. The versatility of the technique allows for the application of various design styles, from sophisticated and elegant to fun and playful. IMD enables silicone to transcend its functional purpose and become a true embodiment of artistry. Join us as we continue our exploration of the transformative power of IMD in the world of silicone product manufacturing.
IV. Seamless Integration of Decoration and Functionality
A. How IMD Allows for the Simultaneous Incorporation of Design and Functionality in Silicone Products
One of the remarkable aspects of In-Mold Decoration (IMD) is its ability to seamlessly integrate decorative elements while preserving the functionality of silicone products. IMD offers a harmonious union of design and purpose, where aesthetics and practicality coexist in perfect balance. By applying the decoration during the molding process, IMD ensures that the design becomes an integral part of the silicone item, without compromising its functionality or usability. Whether it’s buttons, grips, or protective cases, IMD enables the simultaneous incorporation of stunning visuals and essential features, making silicone products both visually appealing and highly functional.
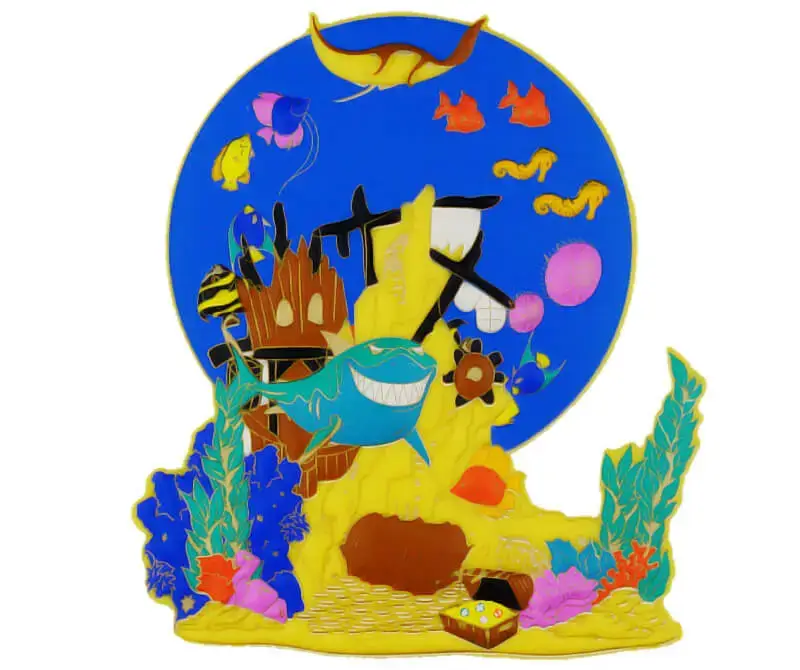
B. Examples of IMD-Enhanced Silicone Products with Functional Features
Let’s explore some examples of silicone products enhanced by IMD, showcasing how design and functionality seamlessly come together:
- Smartwatch Bands: IMD can transform ordinary silicone smartwatch bands into fashionable accessories with eye-catching designs. By integrating intricate patterns, textures, or even branding elements directly into the silicone material, IMD enhances the aesthetic appeal while retaining the flexibility, durability, and comfort that silicone bands offer. The result is a smartwatch band that not only looks stylish but also provides a secure and comfortable fit for everyday wear.
- Control Buttons and Keypads: IMD takes silicone control buttons and keypads to a new level of sophistication. The technique allows for the incorporation of tactile feedback elements, ensuring precise and responsive functionality. Whether it’s a car dashboard, a remote control, or a medical device interface, IMD can enhance the user experience by providing visually pleasing designs while maintaining the necessary functionality and tactile response.
- Protective Phone Cases: IMD brings a delightful fusion of design and protection to silicone phone cases. The technique allows for the integration of attractive patterns, vibrant colors, or even personalized graphics, all while maintaining the shock-absorbing and impact-resistant properties of silicone. IMD-enhanced phone cases not only safeguard the device but also reflect the unique style and personality of the user.
These examples showcase how IMD seamlessly integrates decoration and functionality in silicone products. IMD enhances the visual appeal without compromising the essential features, resulting in products that captivate both the eyes and the senses. As we delve deeper into the world of IMD, we will explore more instances where design and functionality converge, creating silicone products that are both aesthetically pleasing and highly practical.
V. Durability and Longevity

A. Discussing the Protective Properties of IMD for Silicone Products
When it comes to silicone products, durability is paramount. In-Mold Decoration (IMD) not only enhances the aesthetics but also provides an added layer of protection, ensuring the longevity of the decorative elements. IMD creates a robust and durable bond between the design and the silicone material, offering exceptional protection against daily wear and tear. The design is encapsulated within the silicone, shielding it from external factors such as moisture, chemicals, and UV radiation. This protective barrier safeguards the decoration, preserving its vividness and integrity over an extended period. Whether it’s a smartphone case exposed to frequent handling or a kitchen utensil used in rigorous culinary preparations, IMD ensures that the decorative features remain vibrant and resistant to damage, ensuring the longevity of the silicone product.
B. Highlighting the Resistance to Wear, Scratches, and Fading
IMD enhances the durability of silicone products by providing remarkable resistance to wear, scratches, and fading. The design infused into the silicone through IMD becomes an integral part of the product, eliminating concerns about peeling, flaking, or rubbing off over time. The protective layer of silicone surrounding the design acts as a shield, minimizing the impact of scratches and abrasions that commonly occur during daily use. Furthermore, IMD utilizes high-quality inks and materials that are resistant to fading caused by exposure to sunlight or harsh environmental conditions. This ensures that the decorative elements retain their vibrancy and visual appeal, maintaining the original aesthetics of the silicone product for an extended period.
With IMD, silicone products become not only visually captivating but also incredibly durable and long-lasting. The technique provides a protective layer that shields the decorative elements from the rigors of everyday use, ensuring that the design remains intact and vibrant. Join us as we delve deeper into the resilient nature of IMD and its ability to preserve the beauty and longevity of silicone products, making them reliable companions for years to come.

VI. Applications of IMD in Silicone Products
A. Consumer Electronics: IMD’s Role in Enhancing Silicone Phone Cases, Smartwatch Bands, etc.
In the realm of consumer electronics, In-Mold Decoration (IMD) plays a pivotal role in elevating silicone products to new heights. Silicone phone cases and smartwatch bands, for example, benefit greatly from IMD’s ability to seamlessly integrate captivating designs. IMD enables the application of intricate patterns, textures, graphics, and even branding elements directly onto the silicone surface, enhancing the visual appeal of these accessories. The result is a marriage of style and protection, where silicone phone cases and smartwatch bands become fashionable expressions of personal taste while safeguarding the devices they adorn.
B. Automotive Industry: IMD Applications in Silicone Dashboard Elements, Buttons, etc.
The automotive industry has also embraced the transformative power of IMD in silicone products. Silicone components used in vehicle interiors, such as dashboard elements and buttons, can be enhanced through IMD. The technique allows for the incorporation of sleek metallic finishes, woodgrain textures, or custom designs onto the silicone surfaces, adding an element of sophistication and elegance to the car’s interior. IMD not only enhances the aesthetics but also ensures the durability and functionality of these silicone components, making them a visually pleasing and integral part of the automotive experience.
C. Household Appliances: How IMD Transforms Silicone Kitchenware and Home Accessories
In the realm of household appliances, IMD brings a touch of elegance and style to silicone kitchenware and home accessories. Silicone spatulas, utensils, coasters, and other items undergo a remarkable transformation through IMD. Intricate designs, patterns, or even personalized graphics can be seamlessly integrated onto the silicone surfaces, enhancing the visual appeal of these everyday essentials. IMD allows silicone products to become eye-catching decorative elements in the kitchen or around the house, adding a dash of personality and charm to the living space.
The applications of IMD in silicone products span various industries, from consumer electronics to automotive and household appliances. By harnessing the artistic potential of IMD, manufacturers can create silicone items that are not only functional but also visually captivating. Join us as we explore further examples of IMD applications, unveiling the remarkable ways in which this technique is shaping the world of silicone product manufacturing.
VII. Future Trends and Innovations
A. Emerging IMD Techniques and Technologies for Silicone Products
As the world of manufacturing continues to evolve, new and exciting techniques are emerging to further enhance the aesthetics of silicone products through In-Mold Decoration (IMD). One such innovation is the integration of augmented reality (AR) and virtual reality (VR) technologies into the IMD process. This allows designers and manufacturers to preview and fine-tune the placement of designs in a virtual environment before the actual production, ensuring precise and optimal results. Additionally, advancements in printing technologies, such as high-resolution inkjet printing and digital direct IMD, offer improved accuracy, color vibrancy, and intricate detail reproduction, opening up even more possibilities for stunning visual effects on silicone surfaces. These emerging techniques and technologies are poised to revolutionize the way silicone products are decorated, pushing the boundaries of imagination and captivating consumers with their immersive and lifelike designs.
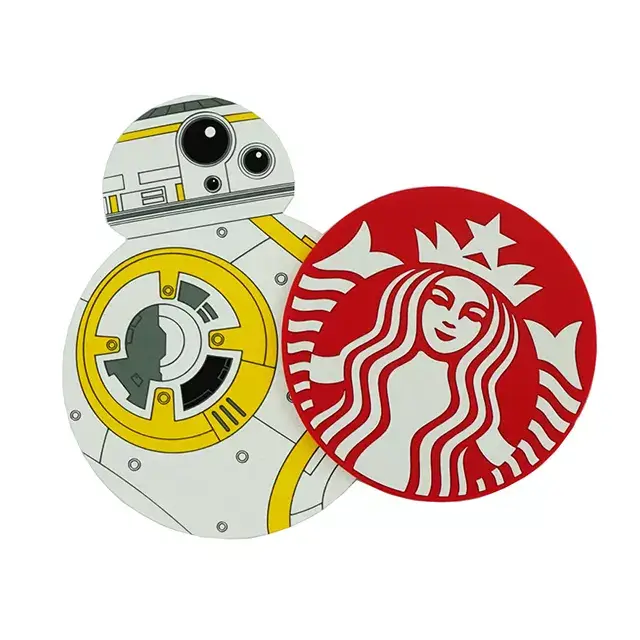
B. Potential Advancements and Possibilities for Further Enhancing Silicone Aesthetics
Looking ahead, the future holds promising advancements and possibilities for further enhancing the aesthetics of silicone products through IMD. One exciting area of exploration is the integration of smart and interactive elements into silicone surfaces. Imagine silicone products with embedded LED displays, touch-sensitive controls, or even dynamic color-changing capabilities. IMD can facilitate the integration of such functional and interactive features without compromising the visual appeal or durability of the silicone material. Additionally, the use of advanced materials, such as self-healing or self-cleaning coatings, can be combined with IMD to enhance the longevity and maintenance of the decorative elements. Furthermore, the customization and personalization of silicone products through IMD are expected to grow, with the ability to create one-of-a-kind designs or even allow users to customize their own patterns and graphics.
With the continuous advancement of technology and innovative approaches, the future of IMD in silicone products is poised to be even more captivating and transformative. As manufacturers and designers embrace these advancements, silicone products will not only serve their functional purposes but also become artistic expressions that delight and engage consumers on a deeper level.
Join us as we explore the exciting future trends and innovations in IMD for silicone products, uncovering the possibilities that lie ahead and the remarkable transformations that await us.
VIII. Conclusion
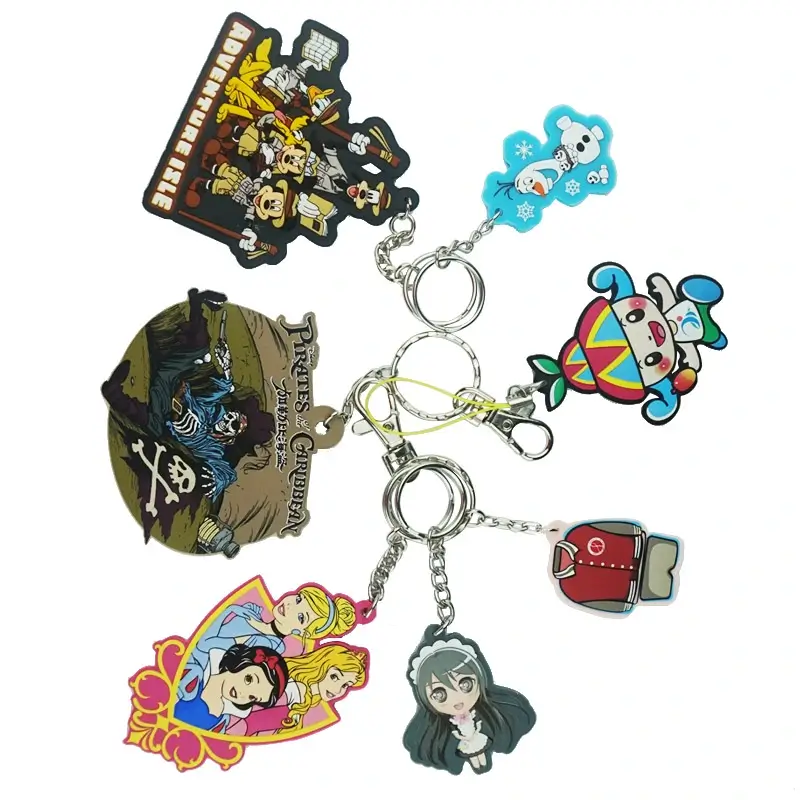
A. Recap of the Benefits and Impact of IMD on Silicone Products
In conclusion, In-Mold Decoration (IMD) has revolutionized the world of silicone product manufacturing, offering a multitude of benefits and significantly impacting the aesthetics, functionality, durability, and longevity of silicone items. IMD allows for the seamless integration of captivating designs onto silicone surfaces, transforming them into visually stunning works of art. By preserving the functionality and protective properties of silicone, IMD ensures that these decorative elements remain vibrant and resistant to wear, scratches, and fading over time. The technique opens up a world of design possibilities, enabling intricate patterns, textures, gradients, and even 3D effects. From consumer electronics to automotive components and household appliances, IMD has found its place across various industries, enhancing the appeal and value of silicone products.
B. Final Thoughts on the Artistic Potential and Future Prospects of IMD in Silicone Manufacturing
The artistic potential of IMD in silicone manufacturing is boundless. As technology continues to advance, we can expect to see further innovations in the field, such as the integration of augmented reality, advanced printing techniques, and interactive elements. These developments will enable designers and manufacturers to push the boundaries of creativity and deliver silicone products that not only fulfill their functional roles but also captivate with their visual allure. The future prospects of IMD in silicone manufacturing are exciting, with the potential for customizations, personalized designs, and even smart features embedded within silicone surfaces.
As we reflect on the journey through the world of IMD and its impact on silicone products, we are reminded of the remarkable transformation that occurs when artistry meets functionality. IMD has not only elevated the aesthetics of silicone but also enhanced its durability, protection, and versatility. The possibilities are endless, and we eagerly await the continued exploration and realization of these possibilities in the future.
Join us in embracing the artistic potential of IMD in silicone manufacturing, where design, innovation, and craftsmanship converge to create silicone products that inspire, delight, and enrich our lives.